A eficiência operacional é essencial para garantir a produtividade e a segurança dos processos. Um dos aspectos fundamentais para alcançá-la é o monitoramento contínuo da corrente e da tensão elétrica dos ativos.
Essa é uma prática que fornece insights valiosos sobre o estado de funcionamento dos equipamentos e também desempenha um papel vital na prevenção de falhas, na otimização da manutenção e na redução dos custos operacionais.
Neste artigo, entenda como funciona o monitoramento de corrente e tensão, como ele ajuda a evitar falhas e as principais ferramentas utilizadas. Acompanhe!
O que é monitoramento de corrente e tensão?
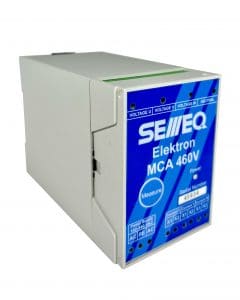
O monitoramento de corrente e tensão elétrica é uma prática fundamental na gestão de ativos elétricos em uma planta industrial. Ele consiste na análise contínua das informações de potência, tensão e corrente, permitindo um diagnóstico preciso do estado operacional dos equipamentos.
Ao acompanhar regularmente esses parâmetros, é possível identificar eventuais fugas de corrente, instabilidades, distorções e surtos elétricos, fornecendo insights valiosos para a gestão da manutenção.
A manutenção preditiva baseada no monitoramento de corrente e tensão é crucial, uma vez que problemas não detectados nesses equipamentos podem resultar em danos irreversíveis, levando à necessidade de substituição e causando prejuízos significativos.
Além disso, a análise desses dados ajuda a evitar sobrecargas perigosas que podem comprometer todo o fluxo produtivo a longo prazo.
Como a corrente e a tensão afetam o desempenho e a vida útil dos equipamentos?
A corrente elétrica é a quantidade de carga elétrica que flui através de um condutor em um determinado período de tempo, enquanto a tensão elétrica é a diferença de potencial elétrico entre dois pontos de um circuito.
Ambos os parâmetros têm impacto direto no desempenho e na integridade dos equipamentos. Entenda:
- Desempenho: a corrente fornece a energia necessária para alimentar os equipamentos, enquanto a tensão determina a quantidade de energia disponível para realizar o trabalho. Flutuações excessivas na corrente ou na tensão, por exemplo, podem resultar em variações no desempenho dos equipamentos, levando a falhas operacionais, perda de eficiência ou até mesmo paradas não programadas;
- Vida útil: as correntes elétricas fora dos limites especificados podem causar superaquecimento nos componentes internos dos equipamentos, levando ao desgaste prematuro e à redução da vida útil.
Como o monitoramento preventivo pode evitar falhas catastróficas
Ao implementar sistemas de monitoramento de corrente e tensão, é possível identificar precocemente quaisquer anomalias ou tendências preocupantes nos padrões de operação dos equipamentos, incluindo variações anormais, sinais de desequilíbrio ou picos repentinos.
Com ele, as equipes de manutenção têm a oportunidade de intervir proativamente, realizando ajustes no sistema elétrico ou substituição de componentes defeituosos.
Por exemplo, ao detectar esses problemas em estágios iniciais, eles não evoluirão para falhas mais sérias.
Ao adotar essa abordagem, é possível evitar falhas que resultem em danos severos aos equipamentos, paradas não programadas e interrupções na produção. Além disso, ao antecipar problemas, as empresas podem economizar significativamente em custos de reparo e substituição.
Principais técnicas e ferramentas de monitoramento de corrente e tensão
Com o surgimento das soluções IoT, o Big Data e a evolução da tecnologia dos sensores, o monitoramento de corrente e tensão elétrica passou a ser uma tarefa um pouco mais simples.
Entenda, a seguir, quais são as principais técnicas e ferramentas para esse trabalho.
Sensores de corrente
Esses sensores detectam os sinais de corrente gerados pelos motores em funcionamento. Eles permitem identificar problemas, como sobrecargas, desbalanceamento de corrente e surtos elétricos, fornecendo informações essenciais para a manutenção preditiva dos equipamentos.
Big Data
O Big Data é essencial para o monitoramento on-line de ativos, pois permite coletar e analisar grandes volumes de dados gerados por sensores e máquinas. Essa análise possibilita identificar padrões, tendências e anomalias que podem passar despercebidos em abordagens tradicionais.
Armazenamento em nuvem
O armazenamento em nuvem é fundamental para centralizar os dados coletados em plataformas acessíveis remotamente. Com isso, é possível facilitar a colaboração entre equipes e permitir o acesso aos dados de qualquer lugar e a qualquer momento, aumentando a eficiência operacional.
Internet das Coisas (IoT)
A IoT envolve a conexão de sensores, dispositivos e equipamentos em uma rede inteligente, possibilitando a comunicação contínua entre esses elementos. Essa comunicação em tempo real gera dados valiosos sobre o desempenho dos ativos, permitindo a identificação precoce de anomalias e a otimização das operações.
Machine learning
O machine learning é empregado para desenvolver modelos capazes de aprender com os dados e fazer previsões precisas. No contexto do monitoramento on-line de ativos, ele é utilizado para identificar padrões que indicam falhas iminentes nos equipamentos.
Essas técnicas e ferramentas possibilitam uma abordagem proativa e orientada por dados para o monitoramento de corrente e tensão elétrica, garantindo a operação contínua e bem-sucedida das plantas industriais na era da Indústria 4.0.
Tempo é dinheiro: qual deve ser a periodicidade no monitoramento
Avaliar a periodicidade no monitoramento é um ponto-chave para garantir a integridade e o desempenho dos equipamentos em uma planta. Embora existam várias abordagens nesse sentido, uma estratégia que tem se destacado cada vez mais é o monitoramento contínuo.
Nessa abordagem, os sistemas são configurados para acompanhar constantemente as condições de corrente e tensão em tempo real, oferecendo uma visão constante do funcionamento dos equipamentos, permitindo uma detecção precoce de quaisquer anomalias ou problemas emergentes.
Ao monitorar continuamente, as empresas podem identificar falhas potenciais antes que se tornem problemas sérios, reduzindo, assim, o risco de paradas não planejadas e danos aos equipamentos.
Além disso, o monitoramento contínuo proporciona uma maior tranquilidade aos gestores de manutenção, pois eles podem confiar em dados atualizados e precisos para tomar decisões informadas sobre a gestão dos ativos da planta.
Fale conosco
Se sua empresa busca implementar uma solução de monitoramento contínuo de corrente e tensão elétrica, entre em contato conosco para descobrir como a SEMEQ pode ajudar a impulsionar a eficiência e a confiabilidade de suas operações industriais.