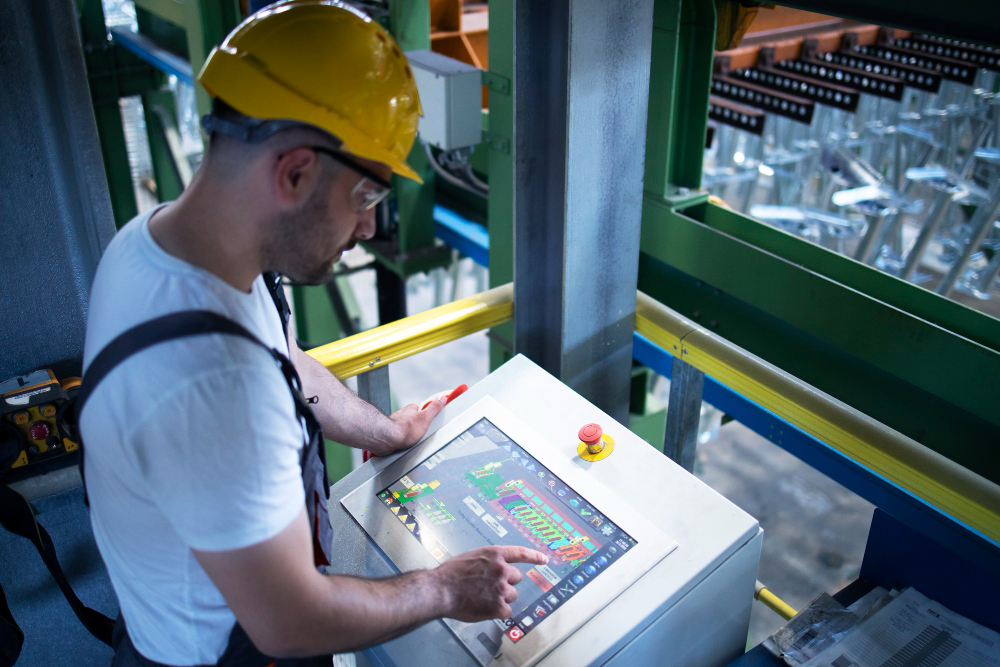
Unlocking the Power of Motor Circuit Ana...
In today’s industrial landscape, electric motors play a...
Read everything71 results in Blog
In today’s industrial landscape, electric motors play a...
Read everythingIn today’s fast-paced industrial environments, where ma...
Read everythingIn the world of industrial operations, manufacturing, a...
Read everythingIn today’s world, where sound quality is critical acros...
Read everythingIn today's technology-driven world, the demand for prec...
Read everything