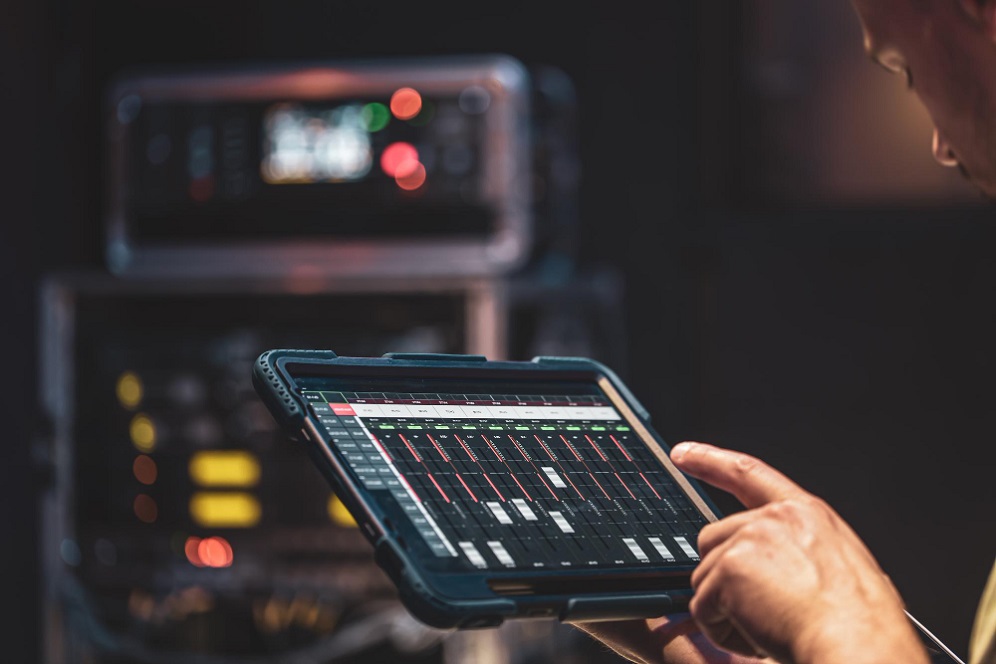
Maximizing Efficiency with Equipment Per...
In today’s competitive industrial landscape, maximizing...
Read everything72 results in Blog
In today’s competitive industrial landscape, maximizing...
Read everythingIn today’s industrial landscape, electric motors play a...
Read everythingIn today’s fast-paced industrial environments, where ma...
Read everythingIn the world of industrial operations, manufacturing, a...
Read everythingIn today’s world, where sound quality is critical acros...
Read everything