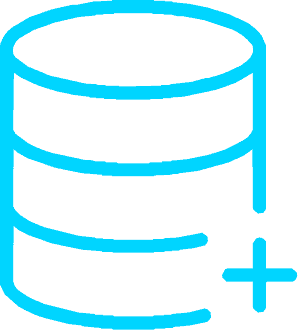
AXON HD VIBRATION AND TEMPERATURE SENSOR
Sensor for predictive maintenance for critical assets
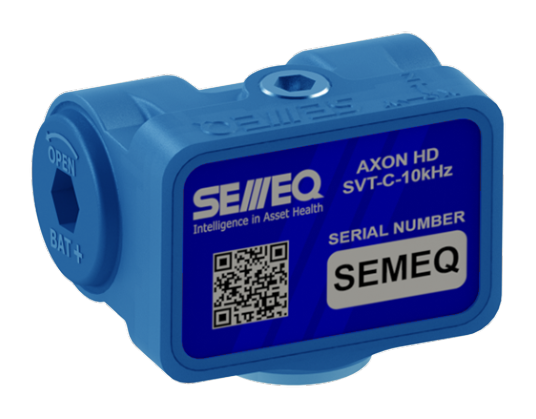
AXON HD 3D Vibration & Temperature
FEATURE:
- Heavy Duty – Extreme resistant to chemical attacks, water and dust
- Triaxial
- FFT, Envelope, Time Wave Form, and Global Levels
- Frequency response: 10 kHz
- Wireless communication Bluetooth® Low Energy 5.1
- Long life battery and replaceable
- IOT Device
- Protection rate: IP 69 K +++
APPLICATION:
- Industrial Pumps, Fans, Reducers, Compressors, Electric Motors, Machine Tools, Turbines
- Early failure detection in bearings and customer cases
User-friendly interface
It has an intuitive user interface that simplifies configuration and daily use.
Durability and Reliability
Designed to operate in harsh industrial conditions, guaranteeing long-term durability and reliability; a robust and effective solution for optimizing maintenance and increasing the reliability of industrial assets.
Request a demo
We offer your company broad and secure forms of data storage.
Click to find out more about this service